I've tried and tried to cast a set of wheels for my M916 project,I found the wheels and try to copy/cast a few but I just can't get the hang of it. Is there anyone out there willing to cast these wheels for me? I provide the masters and of course pay for the resin
thanks
Vince
Scratchbuilders!: Armor/AFV
This is a group for armor scratchbuilding questions, topics and projects.
This is a group for armor scratchbuilding questions, topics and projects.
Hosted by Mike Kirchoff
Help, could I get some one to do some casting

MAD_DUCK

Member Since: March 05, 2002
entire network: 434 Posts
KitMaker Network: 25 Posts
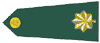
Posted: Monday, May 19, 2003 - 08:37 PM UTC

animal

entire network: 4,503 Posts
KitMaker Network: 1,163 Posts

Posted: Tuesday, May 20, 2003 - 02:55 AM UTC
What type of casting and mold agents are you using? Do you have a one piece mold, or two piece? I cast wheels using a one piece mold I us Smooth-On products. if you will glue a piece of plastic stock to the master wheel. Make the piece a little bit wider then the tire and about as long. Then fasten the wheels to the mold box at the point of the piece that you added to the wheel. pour the mold material at least 1/2 inch around the entire master. After the mold has set completely slit with a very sharp knife blade along the side of the block and down to just past the center of the wheel. You will be able to remove the master and you will have a good mold to cast your tires. When you pour the resin in make sure that you use plenty of releasing agent so you can remove the finished piece. The secret that I found is to not get into a hurry to remove the cast piece. Leave it in the mold for at least twice the recomended time. Anothe trick to make sure that the resin fills the entire mold is to squeeze the mold to distort it and use a long tooth pick to work the resin into all the little areas inside the mold. Be careful and don't jabb the tooth pick too far as to put small holes inside the mold. Blunt the tooth pick's tip a little bit. Try this. Don't be afraid to make mistakes. WE all do it at first. You will get the hang of it in time. By the way Smooth-on products sells a how to vidio and you can get a starter kit with instructions on the basics of mold and resin castings. I don't work for Smooth-On but am a very satisfied customer.




Red4

Member Since: April 01, 2002
entire network: 4,287 Posts
KitMaker Network: 824 Posts

Posted: Tuesday, May 27, 2003 - 04:41 PM UTC
Madduck,
I'm currently away from all my mold making and casing supplies...far far away like in Iraq, but would be willing to help you out when I return if you still need it. The advice that Animal gave is also a good help. Its always better to learn from others mistakes....lord knows I've made many over the years.. lol If you still need help, drop me and I'll be more than happy to help you. Might be awhile before I'm home though. "Q"
I'm currently away from all my mold making and casing supplies...far far away like in Iraq, but would be willing to help you out when I return if you still need it. The advice that Animal gave is also a good help. Its always better to learn from others mistakes....lord knows I've made many over the years.. lol If you still need help, drop me and I'll be more than happy to help you. Might be awhile before I'm home though. "Q"


MAD_DUCK

Member Since: March 05, 2002
entire network: 434 Posts
KitMaker Network: 25 Posts
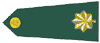
Posted: Tuesday, May 27, 2003 - 06:53 PM UTC
Animal,
The resin and the stuff I use to make the molds is Alumilite. I've been casting the tires as two peice molds, I bluild a box deep enough for the master, pour the mould halfway and let it set. and then I pour the top half and once it sets I cut holes to pour the resin in and one for a air hole. The main problem I am having is that the tires I cast, I can't get two alike, for the most part the tred on the tires won't come out right, they all look like falling apert retreads.
I know that pratice makes perfect,but with my buget I can't keep screwing them up. Now if I can find something cheaper to use instead of Alumilite, then I could give it another try
Vince
The resin and the stuff I use to make the molds is Alumilite. I've been casting the tires as two peice molds, I bluild a box deep enough for the master, pour the mould halfway and let it set. and then I pour the top half and once it sets I cut holes to pour the resin in and one for a air hole. The main problem I am having is that the tires I cast, I can't get two alike, for the most part the tred on the tires won't come out right, they all look like falling apert retreads.
I know that pratice makes perfect,but with my buget I can't keep screwing them up. Now if I can find something cheaper to use instead of Alumilite, then I could give it another try
Vince

Red4

Member Since: April 01, 2002
entire network: 4,287 Posts
KitMaker Network: 824 Posts

Posted: Thursday, May 29, 2003 - 06:51 PM UTC
Duck.. Here is my method of making my molds and casting my parts. Like yourself I started off using Alumilite. I found it cured to quick for what I was doing and have since found other brands to use. Smoothon, like Animal mentioned happens to be one of many. Heres what I do.
1. Use modeling clay to establish an anchor to put your master in. I use crayolla brand. but any type will work.
2. roll the clay out on a small pane of glass about 1/2 again as thick as the master is. example, if your master is 1" thick, make the clay 1 1/2" thick.
3. Use legos building blocks to construct the retaining wall for the molding rubber. Leave adequate space around the edges of the master.
4. You can trim any excess clay away from the edges of the clay so the legos will fit tightly around it.
5. make sure there is no gaps in the lego blocks or between the clay and the blocks. If there are any gaps, they can be filled/plugged with rubber cement.
6. firmly imbed your master 1/2 way into the clay.
7. mix and pour your mold rubber over the entire piece and let cure.
8. I set mine on the washing maching when its running to help remove air bubble
9. Once its all cured, remove the rubber and clay from the legos and flip it over, be careful not to seperate the master from the rubber you just poured.
10. Add your mold release agent to the already cured rubber and pour the other side
11. Once again let cure.
12. Once everything is fully cured, you can seperate the two halves and cut in your pour spouts and vents.
That pretty much covers my method for two part molds. The trick is to not be intimidated and just try it. This is a good place to get advice as no body wants to waste $$ pouring rubber and casting material all over the place.
Some of the other brands of Resin I use are Resicast, and Pourcast. These two are all I can recall at the moment. Kind of hard remembering what I have when I'm in Iraq.. lol
Hope this helps ya. If you want more info...just holler. "Q" :-)
1. Use modeling clay to establish an anchor to put your master in. I use crayolla brand. but any type will work.
2. roll the clay out on a small pane of glass about 1/2 again as thick as the master is. example, if your master is 1" thick, make the clay 1 1/2" thick.
3. Use legos building blocks to construct the retaining wall for the molding rubber. Leave adequate space around the edges of the master.
4. You can trim any excess clay away from the edges of the clay so the legos will fit tightly around it.
5. make sure there is no gaps in the lego blocks or between the clay and the blocks. If there are any gaps, they can be filled/plugged with rubber cement.
6. firmly imbed your master 1/2 way into the clay.
7. mix and pour your mold rubber over the entire piece and let cure.
8. I set mine on the washing maching when its running to help remove air bubble
9. Once its all cured, remove the rubber and clay from the legos and flip it over, be careful not to seperate the master from the rubber you just poured.
10. Add your mold release agent to the already cured rubber and pour the other side
11. Once again let cure.
12. Once everything is fully cured, you can seperate the two halves and cut in your pour spouts and vents.
That pretty much covers my method for two part molds. The trick is to not be intimidated and just try it. This is a good place to get advice as no body wants to waste $$ pouring rubber and casting material all over the place.
Some of the other brands of Resin I use are Resicast, and Pourcast. These two are all I can recall at the moment. Kind of hard remembering what I have when I'm in Iraq.. lol
Hope this helps ya. If you want more info...just holler. "Q" :-)
![]() |